Why Your Menu API Is Slowing Down Your QSR
A slice of stale bread and foul chicken is my favorite burger - said no one ever. However, in 2018, some QSRs faced backlash after ex-employees revealed that an outlet in Texas was serving chicken 16 days past its expiration date.
Unfortunately, this is not an isolated incident. From moldy pre-packaged foods to leftover hamburger meat, such incidents have tormented the QSR industry for years, leading to revenue and customer losses.
These incidents stem from a legacy inventory management that fails to provide Just-in-Time operations, resulting in spoilage and waste. To solve this problem and ensure PoS doesn’t fail, QSR leaders need to embrace the industry’s motto of speed and efficiency in their inventory management system.
However, the problem remains the same: Many QSRs still rely on legacy systems.
Challenges of Traditional Inventory Management
Finding the right balance in inventory levels is challenging with multiple outlets - too much can result in expired items, and too little can lead to lower sales.
1. Lack of Real-time Inventory Visibility
When tracking inventory across multiple locations, real-time visibility is vital. Traditional systems relying on periodic batch updates lead to inconsistencies and delays in the data flow, making it difficult to identify errors in real time. Many outlets risk having inaccurate stock levels or serving expired food, which can result in health hazards and a loss of reputation.
2. Complex Demand Forecasting
Predicting which menu items to promote in a store in the Philippines during Christmas can be tricky if you don’t have access to relevant data. You need data from multiple sources, like past sales, seasonality, and promotional activities, to make informed decisions.
Due to siloed operations, traditional systems lack the efficiency to unify data.
The result? Last-minute restocking or selling products at heavy discounts.
3. Inefficient Tracking and Management
Manual and periodic checks and updates result in inaccurate sales or inventory level data. This leads to delays in stock replenishment during peak hours.
When a QSR store in Peru runs out of dairy products, their inventory fails to reflect this until the next day. They lose the window to restock, leading to lost revenue.
4. Decentralized System
The behind-the-scenes QSR operation integrates multiple systems, from inventory tracking and supply chain management to PoS. Legacy applications with decentralized systems often lack real-time communication between these systems, resulting in inaccurate stock levels and operational inefficiencies.
5. Limited Resiliency
In QSR, any downtime in your inventory system means delays in orders and unhappy customers. Without built-in fault tolerance, the system is vulnerable to outages during high traffic.
Additionally, a single point of failure means your whole system for the global chain goes down. This lack of resilience can strain QSRs’ daily operations, increasing the IT team’s workload in manually resolving the issue.
6. Poor Scalability
Traditional monolithic systems struggle to adapt to spikes in order volume or transactional load, especially during rush hours or the festive season. This means slow store service, more canceled orders, and frustrated customers.
Solution: Event-Driven Architecture To Overcome Legacy Challenges
Event-driven architecture (EDA) has proved to help organizations achieve operational efficiencies, scalability, agility, and flexibility by decoupling services. For QSRs that depend on cross-application functionality, event-driven architecture ensures that inventory management is always up-to-date and responsive to demand fluctuations.
Here is a use case:
When a customer orders through the PoS system, the inventory automatically adjusts the stock level to reflect the current demand and triggers a supply chain request for restocking. The decoupling of different services means each QSR component responsible for just-in-time operations can operate independently.
The EDA resolves the bottlenecks of coupled applications:
- Operational efficiency: By replacing inefficient communication methods like polling and webhooks, you can reduce CPU usage, leading to lower cost and efficient operations
- Decoupled services: Instead of using a monolithic application that handles all aspects of your inventory, event-driven architecture decouples producers and consumers of events, allowing you to extend QSR functionalities independently.
- Simplify management: The decoupling simplifies management by splitting services for the PoS system, inventory management, and logistics, ensuring that if one service fails, it doesn’t bring down the entire system
- Operational resilience: The event broker stores events when a service is down and delivers them once it is online, ensuring that no data is lost in the event of system outage
The event-driven architecture ensures that the QSR system is responsive and durable even in the face of unexpected outages.
Implementing Event-Driven Architecture using Serverless
Applying AWS Lambda and DynamoDB offers a reliable, scalable, and adaptable inventory management system that keeps everything running smoothly.
AWS Lambda helps QSRs by automating key inventory processes like stock updates, order tracking, and inventory alerts. This relieves store operators from manually checking stocks or the fear of serving expired products.
DynamoDB scales without compromising performance, making it ideal for handling high-volume transactions in a QSR environment. By storing inventory data in DynamoDB, you can ensure high availability, low latency, and automatic scalability. This means your inventory adapts to spikes in traffic without compromising speed and efficiency.
Integrating these AWS functions supports a just-in-time supply chain by providing real-time updates and visibility into inventory. When a new order is placed, DynamoDB triggers AWS Lambda, capturing these changes instantly in the system.
The event-driven architecture reduces the time lag associated with legacy inventory by automating these processes. It allows QSRs to optimize supply chain operations, ensuring fresh ingredients are always available. With back-end functionality being taken care of, store managers can focus on planning menus and serving delicious food to customers.
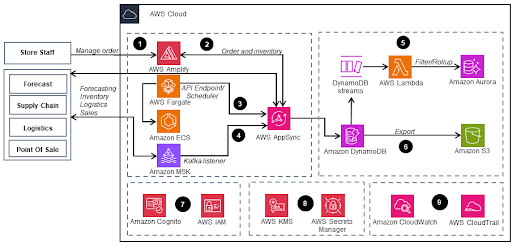
How Integrating AWS Lambda & DynamoDB Optimizes Inventory Management?
A lack of a standardized platform affects the availability, reliability, data quality, and service quality. Integrating AWS Lambda and DynamoDB gives QSR the flexibility to respond to every inventory event, reduce waste, and improve service delivery.
1. Real-Time Inventory Tracking
With AWS Lambda, your system handles events from various sources in real-time
without the need to manage servers. When integrated with DynamoDB’s low-latency data access and global tables feature, the inventory can process updates in real time for your global chain.
When Store C places an order, Lambda functions automatically trigger updates to the inventory stored in DynamoDB, ensuring that stock levels are accurately updated for the day’s operation.
2. System Scalability
DynamoDB handles high-traffic applications by providing single-digit millisecond response times, making it ideal for the fast-paced QSR environment. With Lambda’s automatic scalability, each outlet can efficiently manage inventory demands, especially during rush hours.
3. Cost Efficiency
With serverless infrastructure, QSRs can optimize operational overhead as you only pay for what you use, eliminating the need to pay for unused servers during low-traffic hours.
This allows you to redirect your resources to enhancing customer service and food variety rather than managing IT infrastructure.
4. Data Analytics and Insights
DynamoDB allows you to store and fetch large data volumes quickly, making it easy for QSRs’ outlet managers to track sales trends and inventory levels in real-time. With relevant insights, managers at every outlet can make confident decisions regarding menus and promotional events.
5. Efficient Operations
AWS Lambda and DynamoDB offer built-in resiliency to ensure your QSR runs smoothly even during system disruption. AWS Lambda automatically retries failed actions to complete a process. This means if your system crashes due to an increase in order, Lambda will run the necessary actions, minimizing the impact of the failure.
DynamoDB offers built-in availability and data, ensuring that if a store experiences a failure in one server or region, the rest of your global chain will continue operating successfully.
Key Takeaways
Antstack’s team has helped the engineering teams of QSR brands integrate AWS Lambda and DynamoDB for their inventory management excellence. They leverage serverless to help restaurants respond to stock requirements, avoid waste, and ensure food safety.
Overstocking and understocking harm a restaurant’s bottom line. According to industry reports, poor inventory management systems can cost QSRs $162 billion in revenue annually in the US. An event-driven architecture helps reduce this loss by offering real-time monitoring of inventory levels and a seamless flow of data between core systems.
For more, read the full case study of how Divo TV automated its audio distribution process and enabled data visibility by 90% by going serverless with AntStack.